伺服压力机作为现代智能制造装备的典型代表,凭借高精度、高柔性、智能化等优势,在汽车零部件生产中扮演着关键角色,其重要性主要体现在以下多个维度:
一、高精度加工保障核心零部件质量汽车零部件(如发动机缸体、变速箱齿轮、底盘结构件等)对尺寸精度、表面粗糙度和力学性能要求极高,日本进口DDK伺服压力机的微米级控制精度可满足这类需求:
- 精准位移与压力控制:通过伺服电机驱动滚珠丝杠,位移精度可达±0.01mm,压力控制精度达±1%,确保冲压、锻造等工艺中零件的尺寸一致性(如发动机活塞销孔的公差需控制在5μm以内)。
- 动态响应优势:相比传统液压压力机,伺服压力机的启动/停止响应时间缩短至0.1秒以内,避免惯性冲击导致的零 件变形,尤其适合铝合金、高强度钢等轻量化材料的精密成形(如新能源汽车电池壳体的冲压)。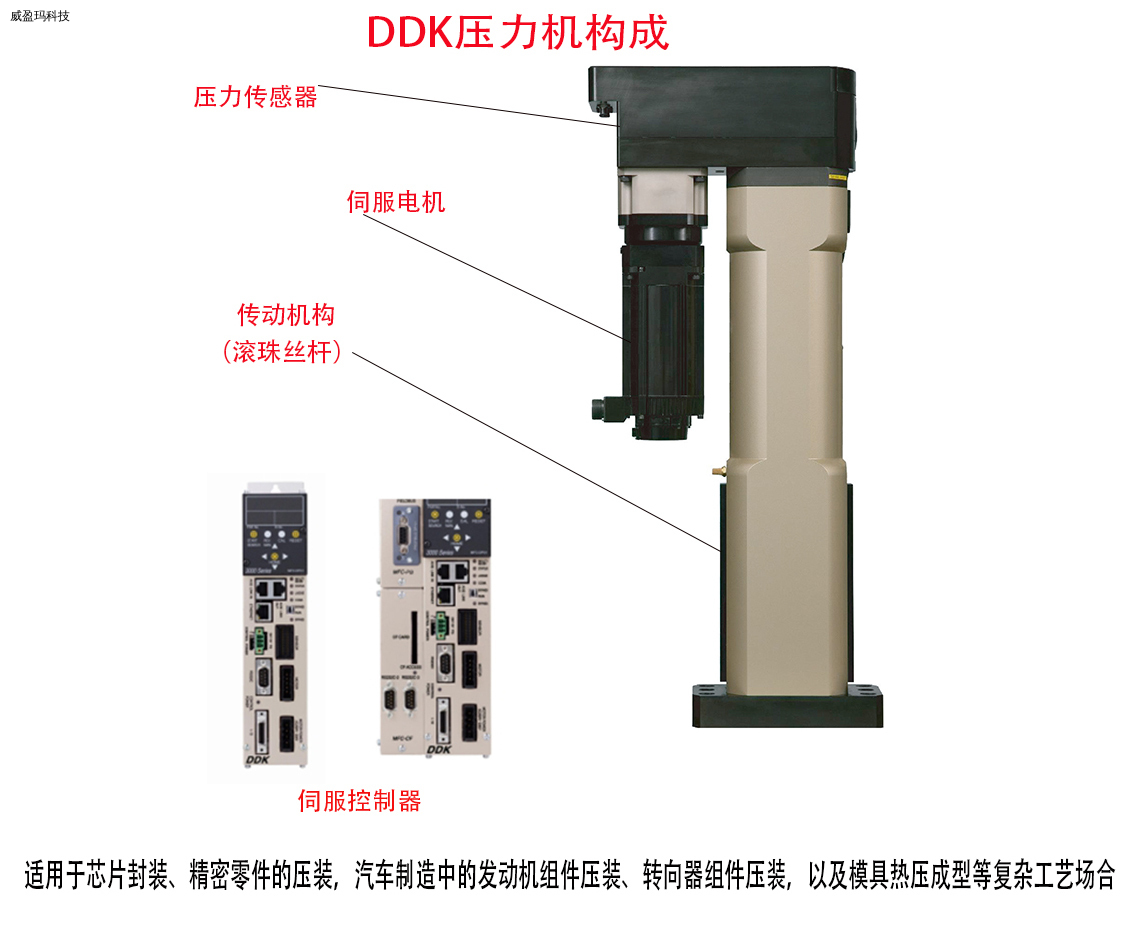
二、高效生产适配汽车行业规模化需求 汽车零部件生产通常需要大规模量产,伺服压力机的高速循环能力和自动化集成可显著提升产能:
- 高节拍生产:日本进口DDK伺服压力机的冲压频率可达200次/分钟以上(传统机械压力机约80次/分钟),配合自动化送料系统,可实现“无人化”连续生产,如车身覆盖件的冲压线效率提升30%。
- 多工序集成:通过伺服系统的多轴联动功能,一台设备可完成拉深、冲孔、翻边等多道工序,减少工件周转时间,例如汽车座椅骨架的生产流程从传统的3台设备缩减至1台伺服压力机。
- 数据:某汽车冲压车间引入伺服压力机后,单班产能从800件/小时提升至1200件/小时,设备利用率提高40%。
三、柔性化生产适应多品种小批量趋势 新能源汽车的发展推动零部件型号多样化,日本进口DDK伺服压力机的参数可编程性使其成为柔性制造的核心设备:
-快速换模与工艺切换:通过伺服系统的参数预设功能,更换模具后可一键调用工艺程序(如压力-位移曲线),换产时间从传统设备的2小时缩短至30分钟,适合新能源汽车电机壳体、电控外壳等多型号零件的混线生产。
- 自适应工艺调整:生产过程中可实时监测压力、位移、温度等数据,并自动修正参数(如补偿模具磨损导致的精度偏差),减少调试时间,例如某车企用伺服压力机生产不同规格的汽车法兰盘,调试效率提升60%。
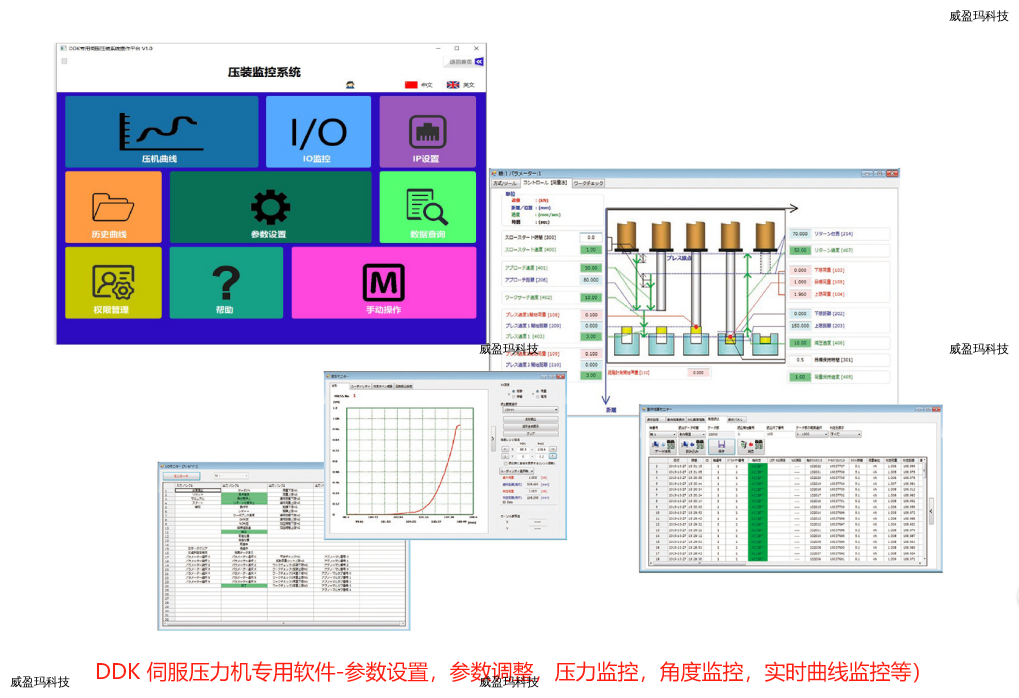
四、节能与环保契合汽车行业绿色转型汽车行业对低碳生产的需求日益迫切,日本进口DDK伺服压力机在能耗和污染控制上优势显著:
- 节能效果突出:伺服电机采用“按需供电”模式,空载功耗仅为传统液压压力机的1/5,生产能耗降低30%-50%。以年产100万件汽车刹车片的产线为例,伺服压力机每年可节电约120万度。
- 低污染与低噪声:取消液压系统,避免液压油泄漏污染,同时运行噪声低于80分贝(传统液压机约95分贝),符合车间环保标准。
五、智能化集成推动汽车制造数字化转型 伺服压力机作为工业4.0的关键节点,可与工厂MES系统、物联网平台深度融合:
- 全流程数据监控:通过传感器实时采集压力、位移、能耗等数据,生成工艺追溯报表(如每件零件的成形曲线),满足汽车行业IATF 16949质量管理体系的可追溯性要求。
- 预测性维护:基于设备运行数据的AI分析,提前预警轴承磨损、电机过热等故障,将停机时间减少50%,例如某汽车零部件工厂通过伺服压力机的智能运维系统,年维修成本降低25%。
-远程调试与优化:支持云端接入,工程师可远程调整工艺参数,例如疫情期间某车企通过远程运维解决海外工厂伺服压力机的工艺异常,避免跨国差旅成本。
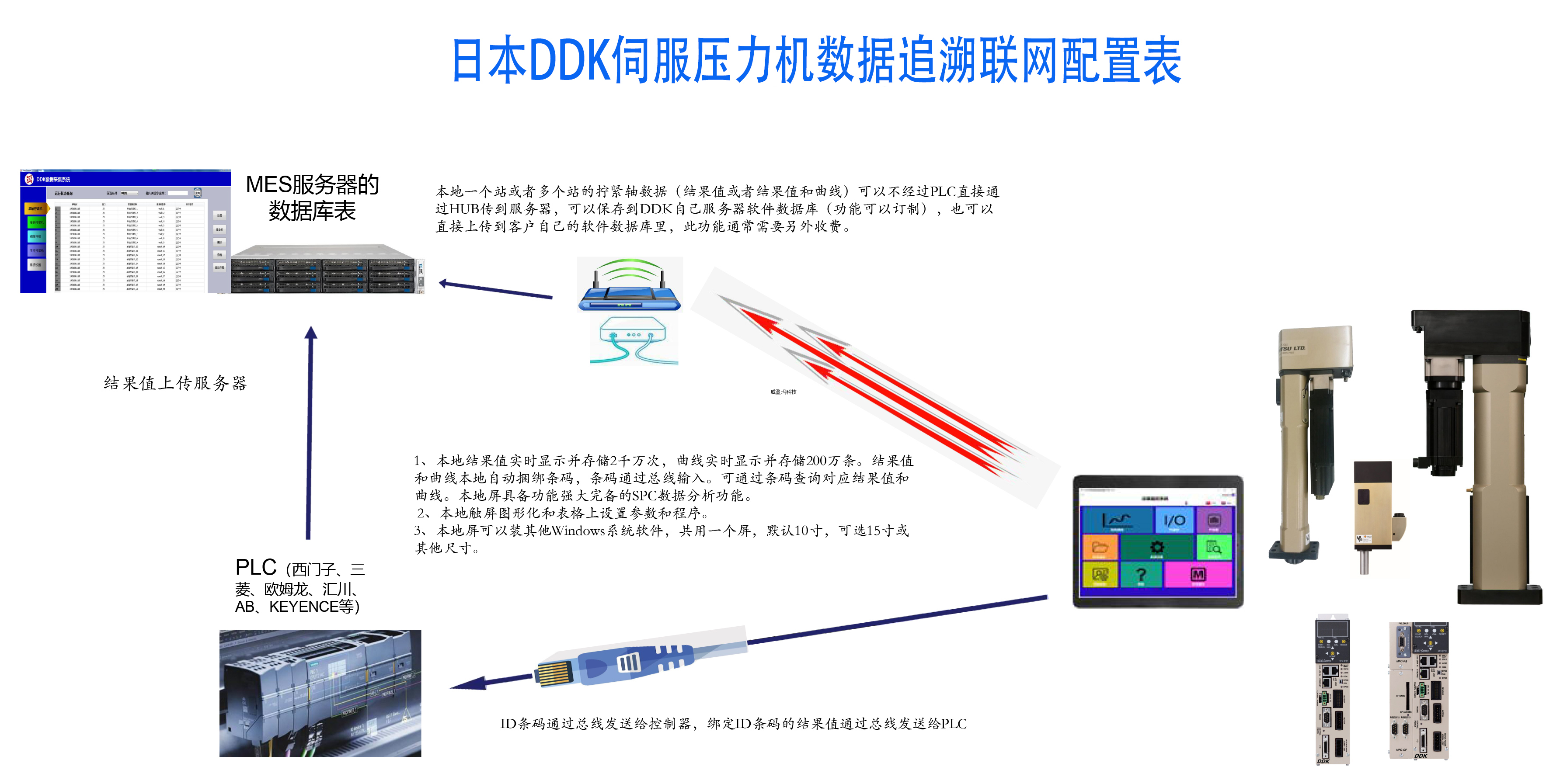
六、特殊工艺赋能汽车新技术落地 新能源汽车的创新零部件(如一体化压铸零件、氢燃料电池极板)对加工设备提出更高要求,日本进口DDK伺服压力机可支撑前沿工艺:
- 精密压铸与挤压:伺服压力机的低速稳定加压特性适用于铝合金半固态压铸,避免传统压铸的气孔缺陷,零件强度提升20%。
- 燃料电池极板成形:氢燃料电池石墨极板的沟槽精度要求达±20μm,伺服压力机通过多段压力控制,可压制出表面粗糙度Ra<1.6μm的高精度流道,保障电池电化学反应效率。
总结:伺服压力机是汽车制造升级的核心装备
从传统燃油车到新能源汽车,日本进口DDK伺服压力机通过精度、效率、柔性、智能 四大维度的突破,不仅解决了汽车零部件生产中的工艺难题,更推动了整个行业向“智能制造”转型。随着汽车轻量化、电动化、智能化的深入,伺服压力机将成为车企提升核心竞争力的关键支撑,其重要性已从单一设备延伸至整个制造体系的优化。