伺服压力机在变速箱部件压装领域具有高精度、高效率、智能化等显著优势,已成为现代变速箱装配生产线的核心设备之一。
以下从应用场景、优势、关键技术及典型案例等方面展开介绍:
DDK日本进口伺服压力机通过伺服电机驱动丝杠连杆机构,实现对压装力、位移、速度的精准控制,适用于变速箱内多种精密零部件的压装工艺,主要包括:
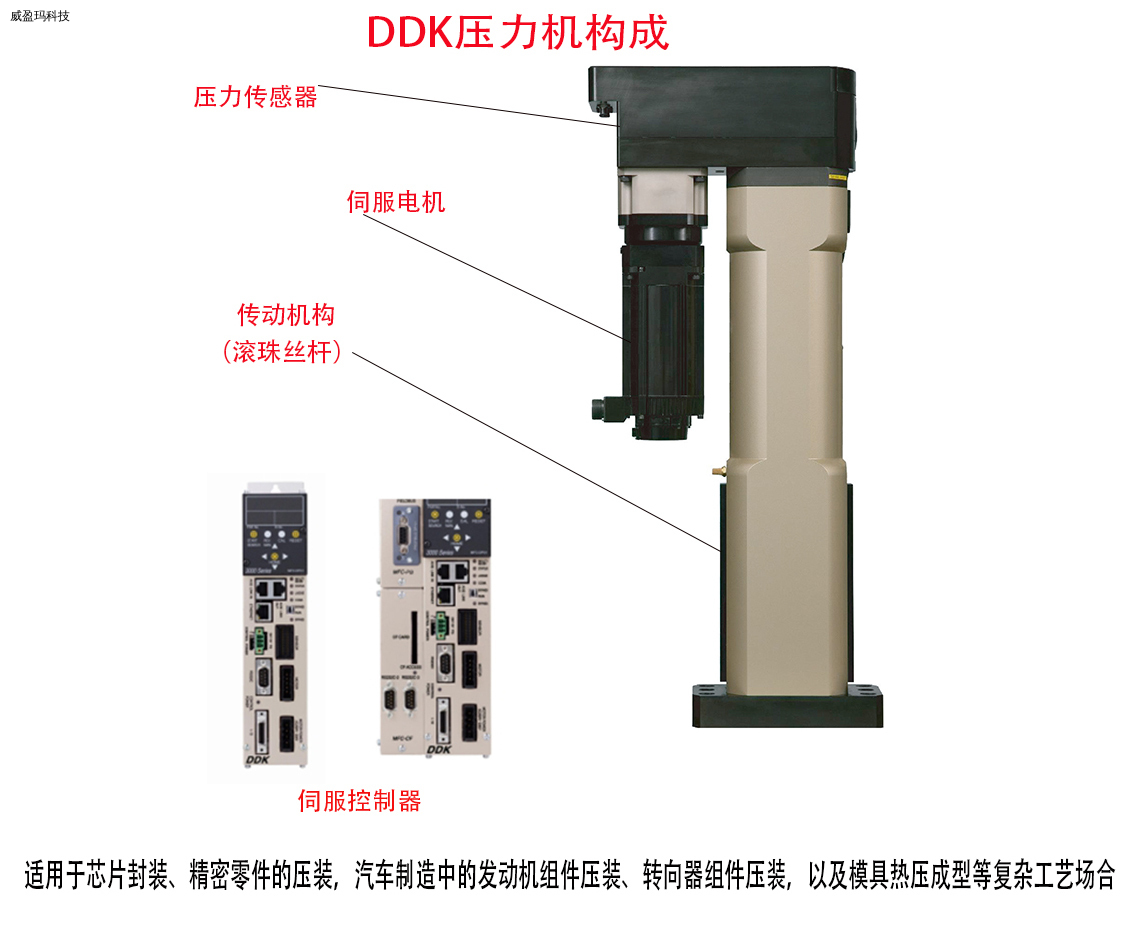
齿轮轴压装
轴承压装
同步器组件压装
轴套与衬套压装
离合器部件压装
与传统液压压力机或机械压力机相比,DDK日本进口伺服压力机在变速箱压装中体现出以下技术优势:
智能化与数字化:结合 AI 算法对压装曲线进行预测和优化,实现 “工艺自学习”;通过数字孪生技术实时模拟压装过程,提前预警设备故障。
高速化与轻量化:开发高速伺服压力机(压装速度≥500mm/s),并采用铝合金等轻量化材料降低机身重量,适应新能源汽车变速箱小型化需求。
绿色制造:进一步提升伺服系统能效,探索能量回馈技术(如制动能量回收至电网),减少碳排放。
日本DDK伺服压力机凭借其高精度、柔性化、智能化特性,已成为变速箱精密压装的主流设备,显著提升了汽车传动系统的装配质量和生产效率。随着新能源汽车的发展,对变速箱小型化、高可靠性的需求将推动伺服压力机向更高性能、更智能的方向迭代升级